Pneumatic Knocker – Type K
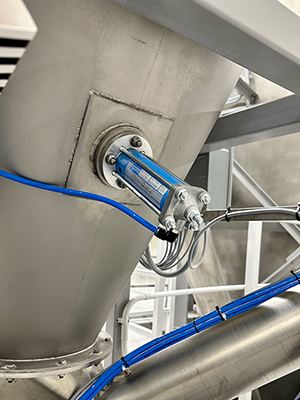
Product properties
Maximum impact effect with the lowest weight
.01application
The Pneumatic Knocker is used for bulk goods with material flow problems, for instance, bridge, siphon and residue formations, when high-speed shakers and vibrators with soft sine-shaped oscillations are no longer effective.
The effect of the knocker is comparable to that of the famous “silo hammer”, but without distorted silo spouts impeding the material flow.
This is because the knocker is only used when it is truly needed: maximum effectiveness with the greatest possible material protection! This relieves the strain on the weld seams, which would otherwise fatigue with constant vibration oscillations.
The knocker is normally controlled by an electrical control system with a solenoid valve.
Within the area where the knocking takes place there should be enough space for the impact to expand in all directions.
Reinforcements of the silo walls and additional ribs should be avoided, as this increases the weight and the strength of the silo walls and thus reduces the effect of the knocker.
The Pneumatic Knocker produces an ideal elastic shock that is specified as the impact energy [Nm] and as impulse [Ns]. There is no impact force or imbalance such as vibrators generate.
The effectiveness of the knocker is evaluated according to the following rule:
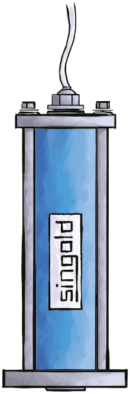
If the product can be knocked off or made to flow with a hand hammer, the Pneumatic Knocker is also effective.
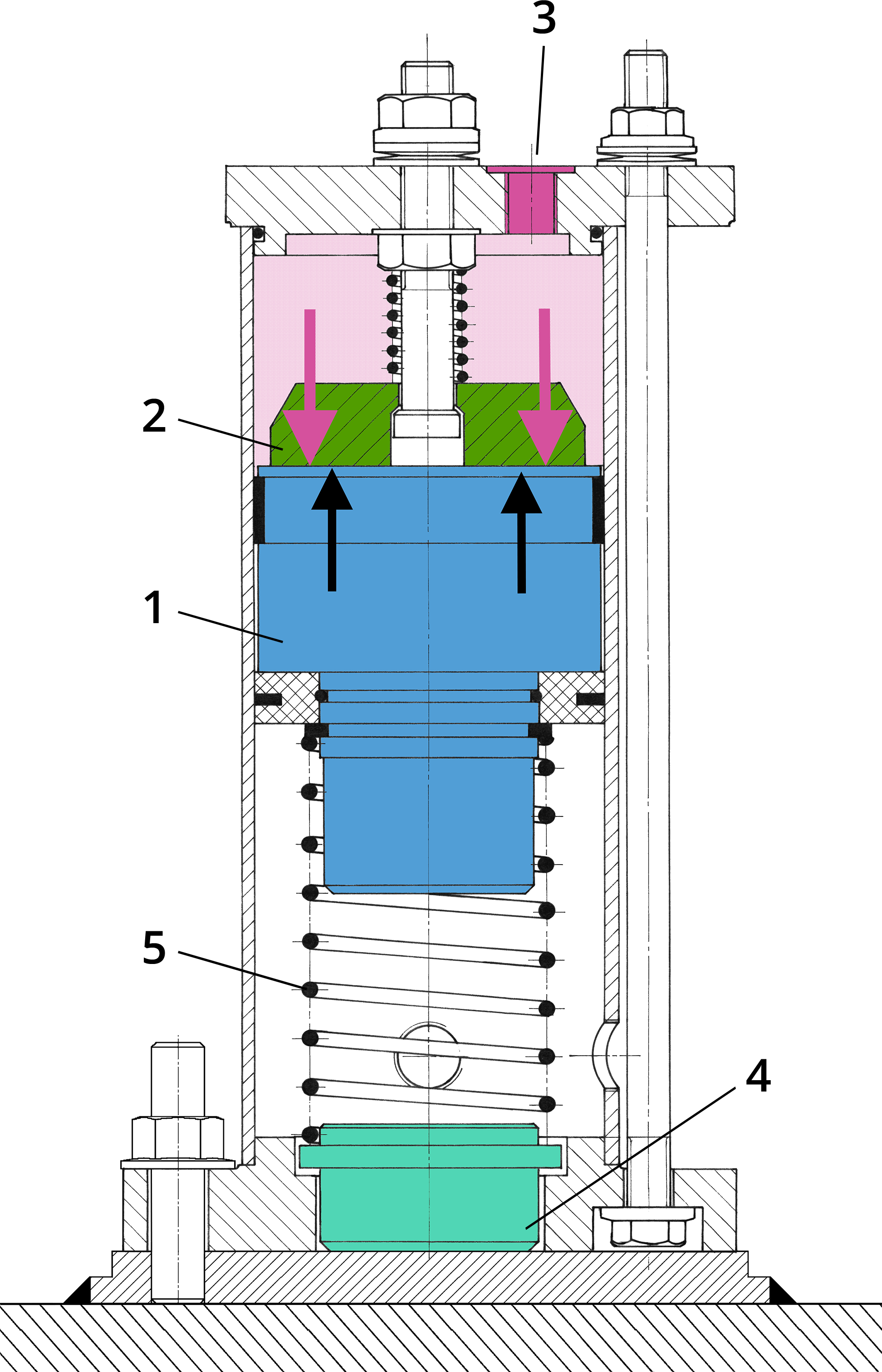
.02Construction & Functioning
With pneumatic singold magnet system knockers, a very high impact work is achieved through spontaneously released stored compressed air energy. In Figure 2 the knocker is shown in section.
The magnetic impact piston (1), designed as a permanent magnet, adheres to the anchor plate (2) in the basic position by means of magnetic force (↑). Compressed air is supplied through the connecting thread (3).
After a short time, the pressure force (↓) overcomes the magnetic force and the magnetic impact piston suddenly detaches itself from the anchor plate.
It is accelerated very forcefully by the stored compressed air and hits the striker bolt (4) with a speed of 6 to 7 m/s. The striker bolt transmits the impact via the welding plate directly to the silo wall.
After venting the knocker, the spring (5) pushes the magnetic impact piston back into its initial position.
.03Sizes & Selection Chart
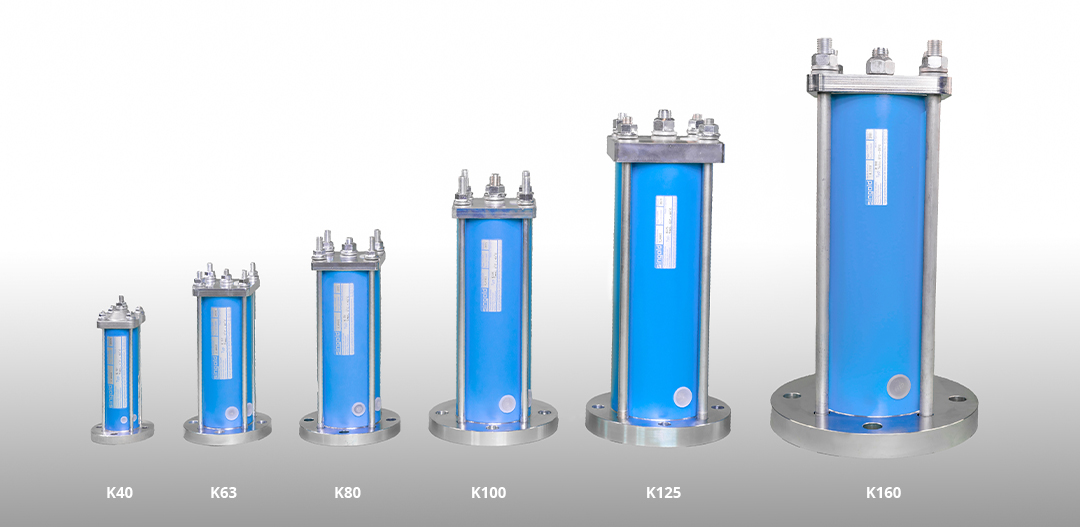
The Selection Chart below provides a rough reference for selecting the adequate size and number of Pneumatic Knockers for round silos of 60° cone. In the case of rectangular containers, a minimum of two knockers are mounted on the flatter sides.
Move your cursor to the desired section (smartphone users will need to click):
Important parameters for the selection of the right knocker:
- Thickness of the container
- Container material
- Container diameter
- Operating temperature
- If present, insulation thickness for the selection of the mounting
- Choice of version in aluminium, steel or stainless steel
- Protection type for operating environment
For the electrical components:
- Desired operating voltage
- Number of knockers
- Protection type for operating environment
For help in selecting the right knocker, please send us the completed questionnaire. Any drawings, sketches or photos of existing plants are also helpful.
.05Mounting & Operation
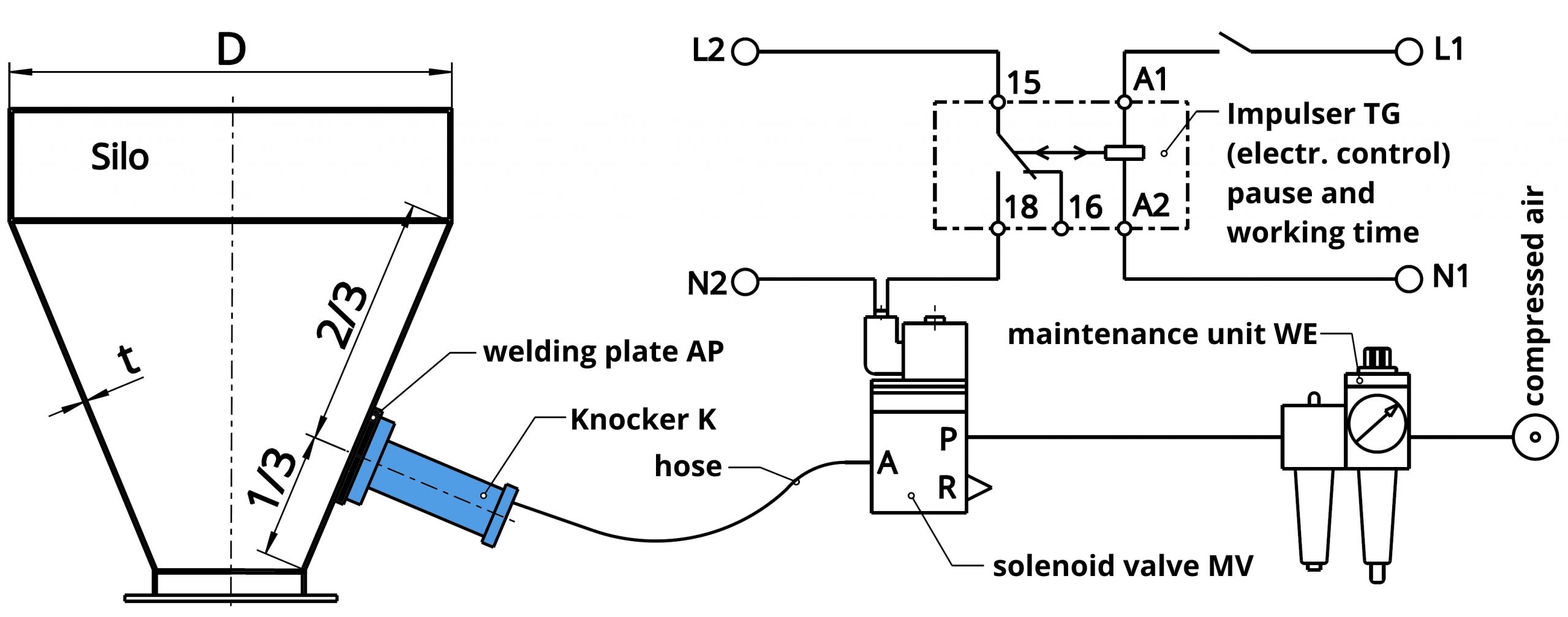
For the assembly and operation of the pneumatic knocker, the components shown in the picture are required:
- Attaching the Pneumatic Knocker Welding plate AP. With small pipes, small containers or containers with insulation welded plate in T-shaped APT
- Pneumatic 3/2 way solenoid valve in the desired control voltage.
- Electrical control for solenoid valve to desired control voltage. An existing PLC control can also be used.
- Pneumatic connectors and cables
- Maintenance unit for pressure reduction to 3.5 bar operating pressure, drainage and lubrication of the knocker is recommended.
Choose the right knocker for your application
We have two types of knockers in our range: our classic ‘singold’ Pneumatic Knocker Type K is suitable for many applications in which the knocker is attached to the silo wall. The special developed Pneumatic Distance-Knocker Type QJ is suitable for knocking from a distance against slow-moving drums and filling or emptying stations with moving containers.
Suitable accessories for
your Pneumatic Knocker.
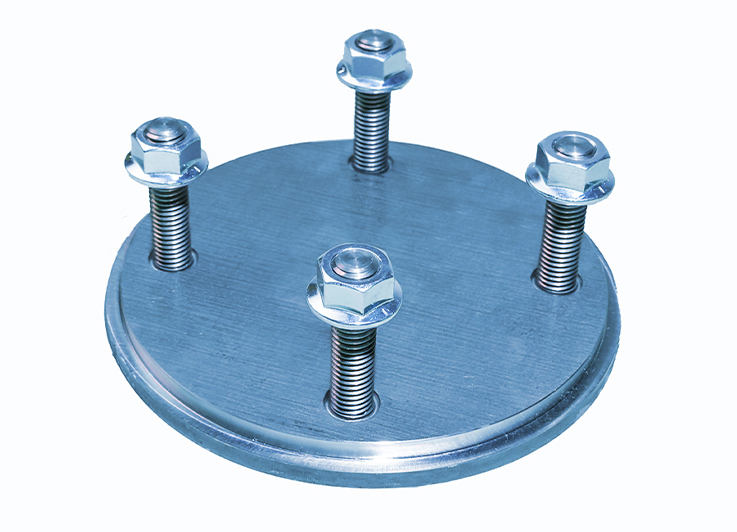
Welding Plates
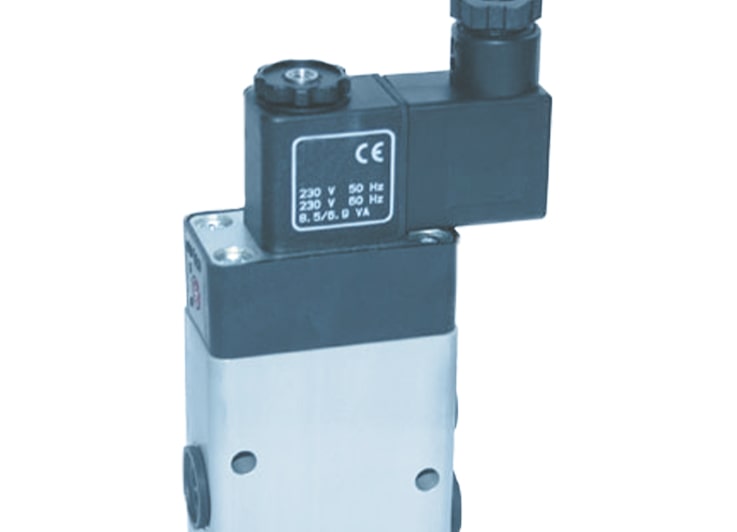
Pneumatic Valves
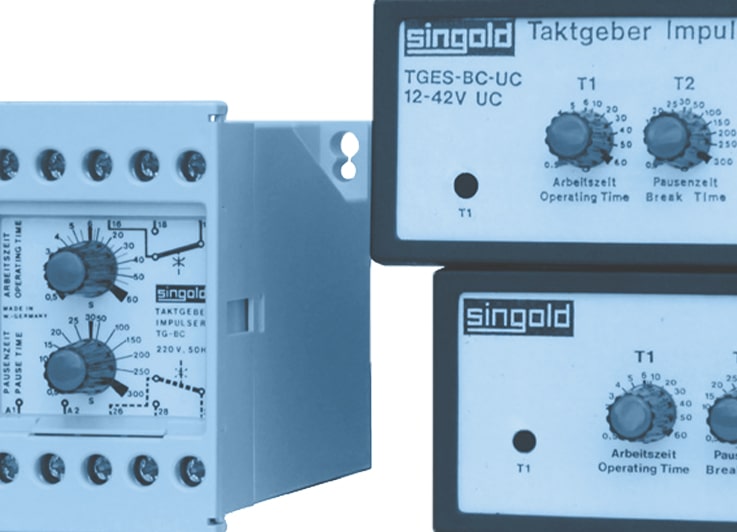
Electrical Controls
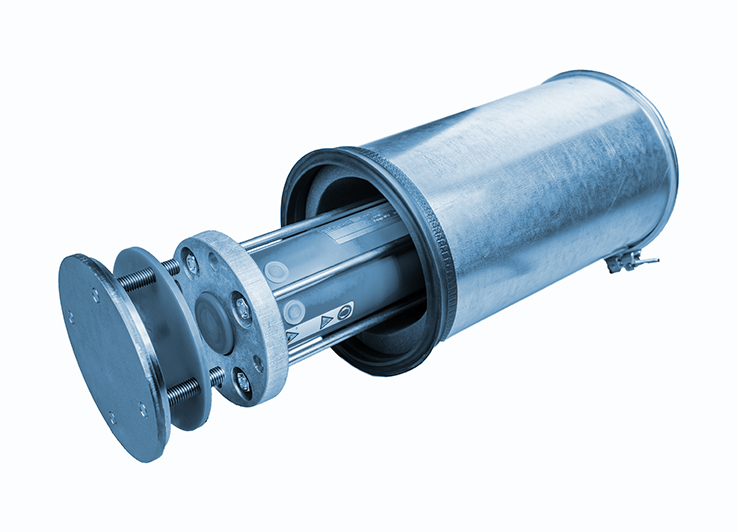
Sound Insulation
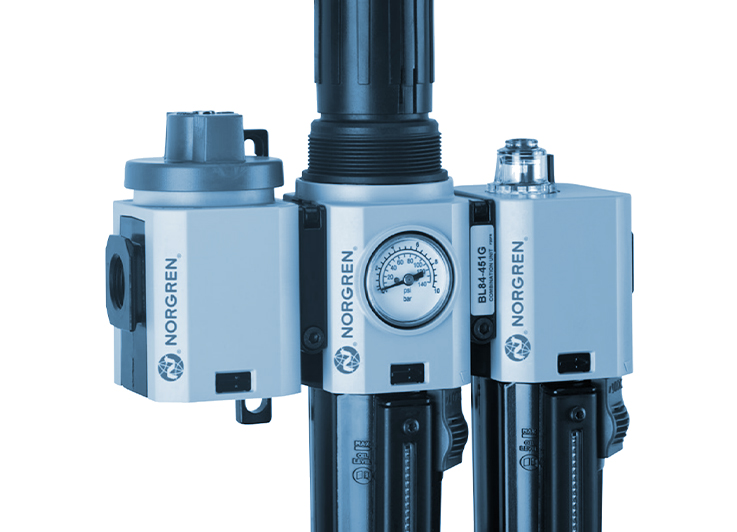
Maintenance Units
We optimise your material flow
Contact us
Taking your individual situation into account, we are happy to assist you.